With the rapid development of the automotive industry, automotive lithium batteries have become a core component of electric and hybrid vehicles.
However, as these batteries are retired, they also bring a problem: how to deal with discarded automotive lithium batteries?
Lithium batteries are mainly composed of positive electrodes, negative electrodes and separators, which contain a large amount of metals and compounds. When the battery is used up, these materials will enter the recycling link. Among them, crushing processing is a key link because it can transform batteries into valuable resources while reducing the impact on the environment. Through the automotive lithium battery crusher, the battery can be broken down into smaller fragments, which can be further processed to extract valuable materials such as metals and plastics. The crushing process can also reduce the impact on the environment because it reduces the space and energy required for landfill or incineration.
In order to ensure the safety and environmental protection of the crushing process, the crushing process of the automotive lithium battery crusher is equipped with a water spray, carbon dioxide fire extinguishing and explosion relief device fire protection system to avoid fire during the crushing process.
Automotive lithium battery crushing is an environmentally friendly resource process that can transform discarded automotive lithium batteries into valuable resources.
Waste lithium-ion battery processing equipment technology, crushing and sorting integrated recycling process.
With the continuous development of science and technology, lithium-ion batteries play an increasingly important role in our lives. However, the generation of a large number of waste lithium-ion batteries has also brought great pressure to the environment. Therefore, the recycling of waste lithium-ion batteries has become a current research hotspot. This article will introduce the crushing and sorting integrated recycling process of waste lithium-ion battery recycling equipment, as well as the recycling methods of positive and negative electrode materials, and briefly describe the waste lithium battery recycling production line.
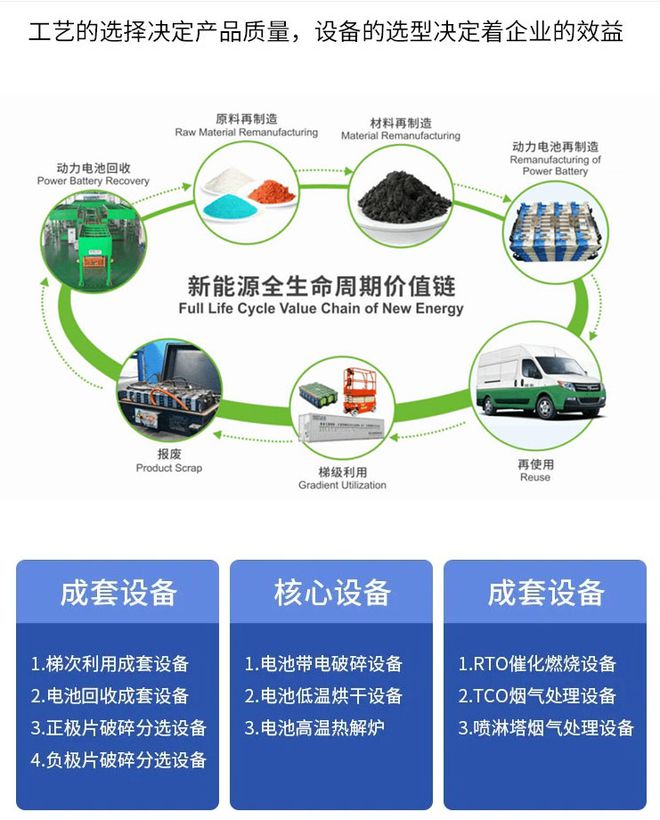
1. Crushing and sorting integrated recycling process
The crushing and sorting integrated recycling process of waste lithium-ion battery recycling equipment mainly includes four stages: pretreatment, crushing, separation and purification, and resynthesis. First, the outer shell and inner core of the lithium-ion battery are separated by simple physical splitting. Then, the battery is crushed to make it into smaller particles. Next, the separation and purification technology is used to separate the positive electrode material, negative electrode material and current collector. Through the resynthesis technology, the recycled materials are made into new battery raw materials to achieve the directional recycling of battery materials.
2. Recycling of positive electrode materials
Positive electrode materials contain metals such as cobalt, nickel, manganese, lithium, iron, and aluminum, and have high recycling value. At present, the recycling of positive electrode materials mainly adopts mechanical grinding. This method separates the positive electrode material from the surface of aluminum foil by mechanical grinding, and then uses chemical methods to separate the elements in the active material. This method has the advantages of simple operation and high recycling efficiency, but there are also some problems, such as high energy consumption and environmental pollution.
3. Recycling of negative electrode materials
The current collector used in the negative electrode of lithium-ion batteries is copper foil, and the negative electrode active material is mainly graphite, hard carbon, soft carbon, etc. These materials also have certain recycling value. At present, the recycling of negative electrode materials mainly focuses on the recycling of copper foil and the reuse of negative electrode active materials. The recycling of copper foil can be separated from the negative electrode material by physical or chemical methods. The reuse of negative electrode active materials can be converted into reusable materials through high-temperature pyrolysis, chemical treatment and other methods.
4. Waste lithium battery recycling production line
The waste lithium battery recycling production line mainly includes feeding system, shredding system, sorting system, diaphragm system, crushing and grinding system and screening system. The feeding system transports the waste lithium batteries to the shredding system, and the batteries are crushed into smaller particles by the shredder and crusher. The sorting system uses airflow air separator and magnetic separator to separate positive electrode materials, negative electrode materials and current collectors. The diaphragm system separates the diaphragm from the battery through the diaphragm box and diaphragm induced draft fan. The crushing and grinding system further crushes and grinds the positive electrode materials and negative electrode materials into smaller particles. The screening system uses linear screens and collectors to screen and classify the crushed materials for subsequent processing and utilization.
In short, the recycling of waste lithium-ion batteries is an important task that can not only reduce resource waste, but also reduce environmental pollution. With the continuous advancement of technology, the recycling technology of waste lithium-ion batteries will become more and more mature, making greater contributions to environmental protection and resource recycling.